Inside Kandui Technologies and UNSW SMaRT Centre's partnership turning waste into sustainable innovation
An interview with Andrew Douglas, Kandui Technologies
This article is part of Circular Sydney, ReCo Digital’s initiative to empower sustainable businesses, supported by the City of Sydney Knowledge Exchange grant. See how it came to life in our case study.
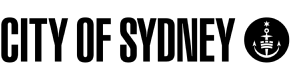
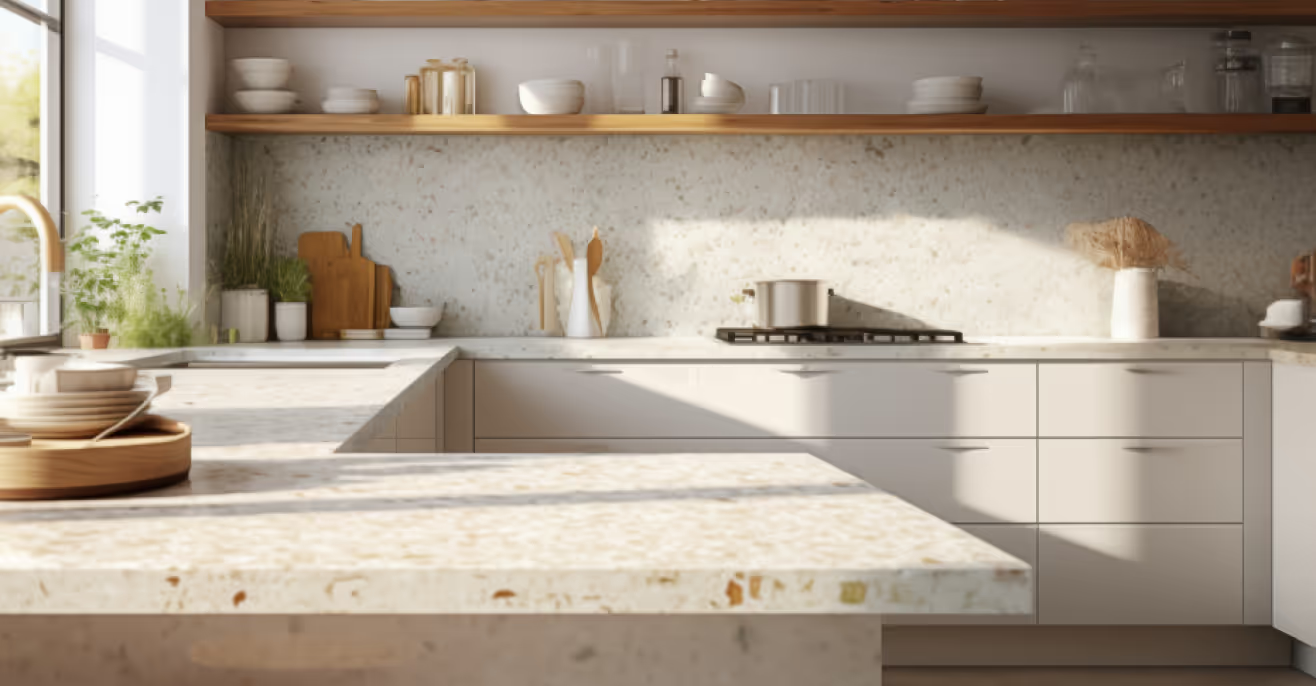
Andrew Douglas has been working with Professor Veena Sahajwalla and Anirban Ghose, bringing Green Ceramics from the lab into the commercial space. In this interview, Andrew shares insights into the challenges and successes of this sustainable venture. He highlights the critical role of partnership in turning innovative ideas into commercial reality.
Can you tell us about Kandui's first product, Green Ceramics?
Green Ceramics is an engineered stone product that's made from waste glass and waste textiles. The technology was invented by Professor Veena and her team at SMaRT@UNSW. We are manufacturing these products in our Nowra MicroFactorie, next to the Shoalhaven Council's glass recycling facility.
The tiles contain between 90 and 95% recycled content. They're hard wearing and strong. They come in different sizes and colours, and are used for floor & wall tiles, island benchtops, tabletops and splashbacks.
Veena and her team didn't only look at waste, but also considered many factors such as the inherent properties and price level—and created something that's even more valuable than the original products the waste comes from. It's amazing to bring them to market.
How did you start working with SMaRT@UNSW?
Many years ago, I was working on mattress recycling and presented at a sustainability conference in Wollongong. That was where I met Professor Veena, who was also presenting at the conference.
I shared with the audience my frustration about recycling the different types of materials in mattresses, especially the mix of synthetic and non-synthetic ones, which are hard to recover.
After the conference, Veena approached me and said, 'I'm really interested in your textile problem. We're doing some research. Would you like to join forces?' I agreed. I thought that was a fantastic journey to be on.
I thought I'd hear back in a month or two, but it took five years of research and development for the university to call and invite me to see their results. That's when I saw the Green Ceramics for the first time—and how Veena and her team transformed the old mattresses into valuable products. They didn't only look great, but also had highly engineered properties.
I was really excited by the first samples. I said, "I want to take this to the market and work with the University to keep improving these products." There's so much we can do to make them perform even better and use more recycled materials.
How long did it take to bring the first sample to market?
In 2021, we set up a pilot plant at Cootamundra to prove the concept. There was a mattress recycling facility out there, so we had all the waste close at hand. We put the equipment in and started the process. The tiles started to pop out at the end of the line. We used up a lot of waste, which was pretty amazing.
From that point, we looked at where we could source waste close to where I am on the south coast here. Shoalhaven Council has a new glass crushing and washing plant at their landfill Nowra. They agreed to let us locate next to their plant. So we have all the glass feedstock coming to us easily. We've gone from a pilot plant in an oversized garage to a medium-size factory that is producing hundreds of squares of tiles every day.
In the beginning, our customers were unsure about using textiles and glass in buildings. They worried about things like fire ratings and strength. So, we had to get our products tested by independent experts to prove they met relevant building codes.
There are many different certifications for different applications, like for floors, walls, and splashbacks. We sent our products to CSIRO and other independent testers. Our products passed these tests and even exceeded many of the standards.
Could you explain the whole process from sourcing the materials to making the products?
The Shoalhaven Council handles the first part of the process. They collect the glass, crush and wash it. We get glass sand, which is important for our product. Glass is strong and hardwearing. It doesn’t have health issues caused by crystalline silica present in other engineered stone products.
We manage the textiles. We gather different kinds of fabrics, like uniforms from schools and government departments. We make sure we have enough materials to keep the process going without stopping. We also keep some extra in case we need to make more tiles in the same style.
Most of the textiles we use are from businesses, which helps us keep things consistent. The colours and materials are the same. We can also use things like sweaters, shirts and T-shirts. We have a way to remove zippers and buttons.
The manufacturing process is different to traditional ceramic tile making. Normally, the tiles are baked at high heat for a long time. Ours are made with high pressure and low heat, so they're faster to make—around three to six minutes per tile.
The energy we use comes from the methane gas produced by the landfill next to us. We don't draw from the electricity grid. There's no fossil fuel in our energy usage.
This is also part of SMaRT@UNSW's MICROfactories approach, and we're also the first licensee of the technologies. The idea is to build small factories near the waste materials and make products for the local area. This saves energy and reduces the carbon footprint from moving tiles around the world.
Can you share some of the projects where the Green Ceramics are used?
We've completed several projects so far. For example, we made tiles for the Sydney Olympic Park aquatic centre, and for various council buildings and sports clubs. We've turned old cricket shirts into tiles for the Lane Cove Cricket Club's rooms, which was pretty cool.
We're working on a large project with a bank. We take the old materials from the building renovation, making them into new tiles, and then putting the tiles back in the refurbishment. This is one of the biggest examples of reusing waste materials from a demolition site and using them again for new products into the same place. It'll take a few years to complete the whole building, and we just delivered our first batch a few months ago.
The cool thing about our Green Ceramics is that when they're no longer needed, we can take them back and use them to make new tiles. This is different from traditional tiles. Our research shows we can do this up to seven times, which adds up to hundreds of years of keeping waste out of landfill.
What factors contribute to success?
We're fortunate to have really smart people at the university who provide us with excellent guidance. It's great to rely on their knowledge and the things they've learned in their research work. This kind of relationship isn't common. Usually, businesses don't work so closely with their research partners.
We've become a part of each other's teams. We have students from the University working with us. And our employees are also at the university, learning about the research process and bringing that knowledge back to our factory.
This setup is beneficial. They create the recipe, and we go into commercial production. We're right at the forefront of making the product better. We can suggest ideas and the guys at uni can test and work on improving them with us.
Another important factor is we have a product that people are willing to buy.
Luckily, with our products, we were able to demonstrate that it was market ready pretty quickly. That gave us a pipeline of people putting deposits and getting income from sales in the early days. While a sustainability grant from the Council and the NSW Environmental Trust helped with some of the equipment and build the facility. We see it as a unique collaboration between UNSW, Shoalhaven City Council, the NSW EPA / Environmental Trust and ourselves.
What challenges have you encountered during this journey?
A real challenge for any commercialisation is to actually make something that the market wants. Design is like fashion. It's constantly changing. What we're selling this year might not be in demand next year.
We can take a blue uniform, shred it up, mix it with glass, and out comes this lovely blue tile. I was happy with the result. But when architects and designers join in, they want different shades, depth and cool shadow effects – these are new for me.
Feedback is great as it pushes us to go further with the product. Without that, the tiles would look quite basic.
Once we've got things sorted out and streamlined, we can customise products for the market. That's what we're doing now. Designers ask us for specific colours, and we create tiles to match. We test and prototype in the lab and show them the results. That's how the product keeps evolving.
What's your vision for Kandui and the manufacturing industry in Australia?
I see a growing sustainability movement in construction, and I believe we're in a unique position to make the most of it. I hope Kandui can be a positive influence on manufacturing in Australia.
We're exploring advanced manufacturing, incorporating things like robotics, sensors, and AI into our processes. We're boldly trailblazing new territory in Australia.
COVID has shown us the importance of Australia's self-reliance. We can't solely rely on outside supply chains. We should start rebuilding our own capabilities, even on a smaller scale, to ensure we're not left stranded if similar challenges arise again. We can be resourceful and do it ourselves.
Our relationship with the university is a great example of how partnerships and collaboration can find great solutions. If we were an island on our own, we wouldn't get this product off the ground. To truly solve problems, we need to build good relationships and work together. When you have that, everything will evolve from there.
Danling Xiao is the co-founder of ReCo Digital. Danling has an unwavering passion for creativity, spirituality and the pursuit of positive change in the world. Connect with Danling on Linkedin.
ReCo LIVE 2025
Join Sydney's purpose-led founders, marketers and innovators to master storytelling, marketing strategies and AI tools.
Artspace, Woolloomooloo
Friday, 1 August, 9am–2pm
100 spots only — don't miss it